New CRV: Efficient Biological Process with Membrane as the Final Stage
One of Europe's most modern treatment plants has taken shape in Kristianstad. A dream project, and on home turf to boot. Together with Kristianstad Municipality, we have built an incredibly efficient wastewater treatment plant that is both ultra-modern with the latest technology and cost-effective.
My name is Åsmund, and I’m from Bardu in northern Norway, but I’ve been living in Kristianstad, Skåne, for 20 years. I ended up here because of my Swedish wife, whom I met when she worked as a nurse in Norway. Since 2018, I’ve been working at NCC’s specialist unit for water and environmental technology. Before that, I spent many years working in construction, civil engineering, and water treatment processes, which has been a great asset in this project.
The central treatment plant in Kristianstad (CRV) is located at Sweden’s lowest point, a few meters below sea level—probably the worst place in Sweden to have a treatment plant. The new plant, which was recently completed, has been built next to the old one and is essentially an entirely new facility. The groundwork was a major challenge: 1,450 piling points with a total of 60 kilometers of piles were driven into the ground to ensure that the new treatment plant stands on a stable foundation.
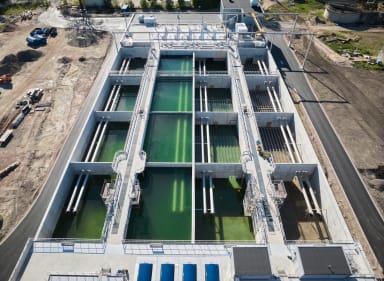
Many Benefits of Building the New Treatment Plant Next to the Old One
Constructing a new facility next to the old one has many advantages. First, it allows for logical and space-efficient construction. Second, it enables optimization of the treatment process, the use of the latest technology, and improvements in energy efficiency. Third, and equally important, it allows for the creation of an excellent working environment. Another major benefit is that the construction of a new facility doesn’t interfere with the operation of the old plant, which continues running as usual until the new one is ready. This significantly reduces project risks!
The new CRV was built as a design-build contract in partnering collaboration with Kristianstad Municipality. Through close cooperation, we collectively achieved the facility that now stands completed. The planning of the new treatment plant was done in 3D, which offers many coordination benefits between designers, NCC, and the client. For instance, the 3D model allowed the operating staff to see how the plant would turn out and provide feedback on the servicing of machinery, in- and outbound transport routes, placement of wash stations, power outlets, and so on. These adjustments were made before construction began, resulting in an optimal facility in every respect.
Water is Pumped Up and Passes Through the Facility by Gravity
Since the treatment plant is located at such a low elevation, the client required that the entire facility be raised to sea level to minimize the risk of flooding. The wastewater enters through three large pressure pipelines from external pumping stations and is channeled upward via vertical pipes to the building where mechanical treatment takes place. From there, the water flows through the facility by gravity.
At the base of the incoming pipes, stones are collected. At the bottom of the vertical pipes, air is injected to remove hydrogen sulfide, which causes workplace and corrosion issues. The hydrogen sulfide is then treated in a deodorization unit. The water is directed into two separate flows through screens and sand traps, where most larger pollutants are removed.
Activated Sludge System with Membrane Filtration
From the sand traps, the water flows by gravity to the pre-sedimentation stage, which consists of eight parallel basins. During temporarily high flows, such as during heavy rain, two basins from the old treatment plant are used as equalization tanks. The water automatically overflows into them when needed and is pumped back after the pre-sedimentation stage once the inflow decreases.
Following pre-sedimentation, the biological stage begins. This is an activated sludge system with four parallel lines and aerated intermediate zones, where the aeration is adjusted based on process conditions and load. Sludge separation is achieved using membrane filters, a relatively uncommon treatment method that is currently used in only a few facilities in Sweden.
The membranes are of the hollow-fiber type—hollow, spaghetti-like threads grouped and secured in elongated modules. Water is drawn through the membranes, from outside to inside, and collected in a pipe from each module. The sludge remains outside the membranes, in the membrane tanks.
The main advantages of this system, called the Membrane Bioreactor (MBR), are that it is more compact than a conventional activated sludge system with sedimentation basins as the final stage and that the membranes produce biologically treated, particle-free water. After the membrane stage, the water flows by gravity through a new pipeline to sand filters for final polishing before the clean water is discharged into Lake Hammarsjön.
Prepared for Pharmaceutical Purification
The new treatment plant, which we expect to last at least 50, possibly 100 years, has been designed with a pedagogical exterior: a brown facade where the water enters and a blue one where the treated water exits. The sludge left over from the process is digested and converted into biogas, which is reused for heating and electricity for the facility.
The plant is also prepared to be upgraded with pharmaceutical purification in the future. Together with Kristianstad Municipality, we tested pharmaceutical purification using activated carbon at a smaller treatment plant in the area. The results were very promising, and depending on future regulatory requirements, the same technology could be implemented at the CRV.
It’s both exciting and a bit bittersweet that the new CRV is now completed. But fortunately, there are many more treatment plants and waterworks across Sweden that need to be rebuilt.